Greetings and salutations!
I come to y'all as more or less an absolute beginner. I have some metalworking experience (MIG welding, knife making, etc) but no engraving. I figured I'd dip my toe in by making myself basic hand gravers (spoiler: its not working out great so far).
[Lest anyone think of suggesting I purchase some tools before attempting to make them: A. I'm unemployed and cannot afford too B. I'm as interested in being able to make my own tools as being able to use them]
I've started with an onglette as it seems the simplest and I have some 1/4" music wire.
I annealed a 6" length of the music wire with a MAPS gas torch then shaped the end to this:
Now I'm guessing I've already made a mistake at this point. Should I have kept the side rounded instead of flattening them?
Proceeding from there I heated the tool up to non-magnetic with the same torch and quenched it in canola oil. Then after removing the fire scale I very carefully torch tempered the tool to light straw.
I decided to test the tool out on some scrap mild steel (most of what I'm making at the moment are knives so being able to engrave those would be great) and it worked for maybe 3cm before I managed to roll the tip.
I'm unsure how to proceed from here as I am not certain if the fault is in the A. geometry of the tool, B. my heat treating process or C. my engraving technique.
A. Geometry
As foreshadowed above should I have kept the sides rounded? In flattening them have I removed too much supporting material from around the tip?
I have checked the face angle and it is very close to 45 degrees. Maybe closer to 47 degrees.
The highest grit stone I've currently got is that 1500 in the background of the first picture. Was my tip maybe no sharp enough? I could glue down some higher grit wet sand paper and buff after if its gotta be really well polished.
B. Heat treat
A MAPS gas torch isn't exactly ideal but its what I currently have on hand. I was really only managing to anneal/harden/temper to first half inch of the wire. I do have access to a forge and could uniformly heat treat the entire length of the tool. I presume this would be best practice but probably not the source of my tip rolling issue?
C. Engraving technique
Honestly I was sort of just going for it. Feeling for an angle that would catch and push a burr. Would using an inappropriate angle have caused the tip to roll?
I'm just using a little ball peen hammer as I don't have an actual engravers (chasing?) hammer.
As for the engraving I was able to do before tip failure this is what I got:
Feedback is very much appreciated. I've had trouble finding clear and accessible resources on engraving. I know there are some killer books out there but my library doesn't have them and they are expensive. I have found some helpful youtube videos out there but most of them don't seem concerned with making the tools (or at least trouble shooting them when they break).
I have more music wire and can start over if those sides really do need to be rounded instead of flat. Can my onglette 1.0 be salvage and maybe just used for softer materials.
I come to y'all as more or less an absolute beginner. I have some metalworking experience (MIG welding, knife making, etc) but no engraving. I figured I'd dip my toe in by making myself basic hand gravers (spoiler: its not working out great so far).
[Lest anyone think of suggesting I purchase some tools before attempting to make them: A. I'm unemployed and cannot afford too B. I'm as interested in being able to make my own tools as being able to use them]
I've started with an onglette as it seems the simplest and I have some 1/4" music wire.
I annealed a 6" length of the music wire with a MAPS gas torch then shaped the end to this:
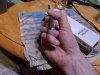
Now I'm guessing I've already made a mistake at this point. Should I have kept the side rounded instead of flattening them?
Proceeding from there I heated the tool up to non-magnetic with the same torch and quenched it in canola oil. Then after removing the fire scale I very carefully torch tempered the tool to light straw.
I decided to test the tool out on some scrap mild steel (most of what I'm making at the moment are knives so being able to engrave those would be great) and it worked for maybe 3cm before I managed to roll the tip.
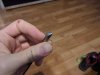
I'm unsure how to proceed from here as I am not certain if the fault is in the A. geometry of the tool, B. my heat treating process or C. my engraving technique.
A. Geometry
As foreshadowed above should I have kept the sides rounded? In flattening them have I removed too much supporting material from around the tip?
I have checked the face angle and it is very close to 45 degrees. Maybe closer to 47 degrees.
The highest grit stone I've currently got is that 1500 in the background of the first picture. Was my tip maybe no sharp enough? I could glue down some higher grit wet sand paper and buff after if its gotta be really well polished.
B. Heat treat
A MAPS gas torch isn't exactly ideal but its what I currently have on hand. I was really only managing to anneal/harden/temper to first half inch of the wire. I do have access to a forge and could uniformly heat treat the entire length of the tool. I presume this would be best practice but probably not the source of my tip rolling issue?
C. Engraving technique
Honestly I was sort of just going for it. Feeling for an angle that would catch and push a burr. Would using an inappropriate angle have caused the tip to roll?
I'm just using a little ball peen hammer as I don't have an actual engravers (chasing?) hammer.
As for the engraving I was able to do before tip failure this is what I got:
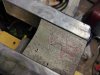
Feedback is very much appreciated. I've had trouble finding clear and accessible resources on engraving. I know there are some killer books out there but my library doesn't have them and they are expensive. I have found some helpful youtube videos out there but most of them don't seem concerned with making the tools (or at least trouble shooting them when they break).
I have more music wire and can start over if those sides really do need to be rounded instead of flat. Can my onglette 1.0 be salvage and maybe just used for softer materials.