rafrisch
New Member
Hey all- First time posting. Great information and wonderful support from fellow engravers on here, it's nice to see!
For my entire 25 year hand engraving career I've always used bent liners, point tools and flat gravers for all the engraving I've done. The vast majority of which were letters and inscriptions on jewelry, trays and trophies. I'm curious if any of you use bent liners for letter "widths" in your engraving? I'd like to learn some new skills, specifically scroll work on knives and guns. Is that even possible without the use of air assist? Being a push hand engraver has limited me to silver, gold and sometimes platinum. Thanks in advance for any thoughts.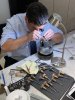
For my entire 25 year hand engraving career I've always used bent liners, point tools and flat gravers for all the engraving I've done. The vast majority of which were letters and inscriptions on jewelry, trays and trophies. I'm curious if any of you use bent liners for letter "widths" in your engraving? I'd like to learn some new skills, specifically scroll work on knives and guns. Is that even possible without the use of air assist? Being a push hand engraver has limited me to silver, gold and sometimes platinum. Thanks in advance for any thoughts.
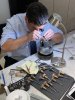