Jeff2t
Member
- Joined
- Jul 23, 2021
- Messages
- 23
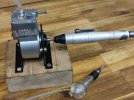
Just remove the motor on the car tyre compressor, fit a spindle through the bearings to attach your Foredom drill and you are set to go.
Build one of these, practice hard, get good, make some money then go out and buy the professional set-up like the Steve Lyndsay Air Graver - that's what I'm trying to do.
YouTube Video