Gargoyle
Official Cafe Stone Carver
I have a couple of questions about this my 1953 Beretta 420bis, the engraved version of the model 418, .25acp.
1. might it be signed anywhere?
2. About how much time would the engraving have taken?
I know on the Beretta shotguns the engravers often signed or initialed their work somewhere near the trigger guard. I can't find anything that could be a signature (I also looked under the grips). Would these have been signed, or was it more of a production line/commercial engraving?
At that time the engraving added very little to the price. Per a 1957 catalog, engraving only added about $6.00 to those sold in the U.S.; Chrome with pearl grips was $43.50, engraved chrome with pearl grips was $49.50. In fact, the upgrade from black plastic to pearl grips (which I suspect were white plastic, not real mother of pearl) added as much to the cost as did the engraving.
(note, Engraved chrome with pearl grips was model 420, the tortoise shell grips make this one model 420bis, which cost more and was rarer.).
I know that 20 years after this was made, in 1974, marble carvers in Italy were earning ₤10,000/day (about $15.00), so I wouldn't be surprised if in 1953, with the postwar economy, engravers in Brescia were getting less than $3.00 per day.
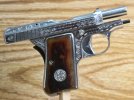
1. might it be signed anywhere?
2. About how much time would the engraving have taken?
I know on the Beretta shotguns the engravers often signed or initialed their work somewhere near the trigger guard. I can't find anything that could be a signature (I also looked under the grips). Would these have been signed, or was it more of a production line/commercial engraving?
At that time the engraving added very little to the price. Per a 1957 catalog, engraving only added about $6.00 to those sold in the U.S.; Chrome with pearl grips was $43.50, engraved chrome with pearl grips was $49.50. In fact, the upgrade from black plastic to pearl grips (which I suspect were white plastic, not real mother of pearl) added as much to the cost as did the engraving.
(note, Engraved chrome with pearl grips was model 420, the tortoise shell grips make this one model 420bis, which cost more and was rarer.).
I know that 20 years after this was made, in 1974, marble carvers in Italy were earning ₤10,000/day (about $15.00), so I wouldn't be surprised if in 1953, with the postwar economy, engravers in Brescia were getting less than $3.00 per day.
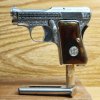
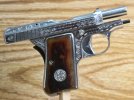