James Roettger
Elite Cafe Member
I use a 2" diameter rubber stopper as a pad when inside engraving. This works well with either hand pushing or pneumatic. The elevated narrow pad allows the hand and fingers easy rotation clearance. It holds the ring well requiring only moderate gripping with the left hand as the cutting pressure alone pushes it down onto the pad. This type of stopper can be found and good mom and pop type hardware stores like Ace, etc. I prefer a 100V angle with 20 degree heel and Lindsay relieving facet geometry on a long narrow graver.
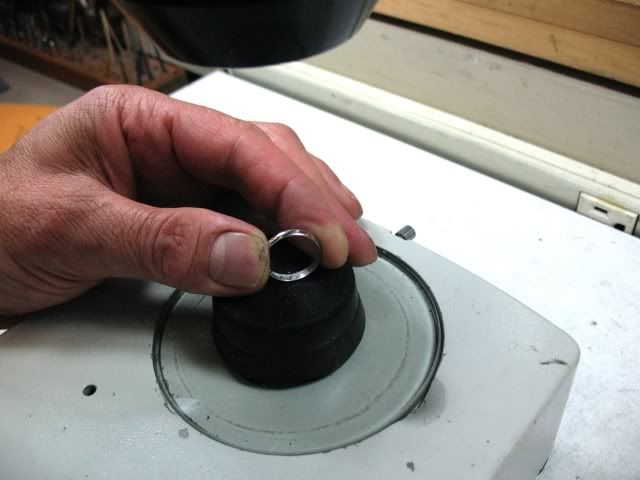
Last edited: