Barry Lee Hands
~ Elite 1000 Member ~
Perhaps this might be of interest to some. . . . .
I took some pics of some things I use in ink transfers, and the results.
Top center: I cut the main scroll and leaf lines in a ring, on the left is the ink, on the right a piece of cardstock, and at the bottom a tape pull of the ink I rubbed into the ring.
After I ink the original piece, I use the card to rub off the excess ink. I then apply clear packing tape, and burnish heavily, to lift the ink.
Then I pull the ink with the tape,
And place it on the next ring, and burnish lightly to transfer the ink,
I took some pics of some things I use in ink transfers, and the results.
Top center: I cut the main scroll and leaf lines in a ring, on the left is the ink, on the right a piece of cardstock, and at the bottom a tape pull of the ink I rubbed into the ring.
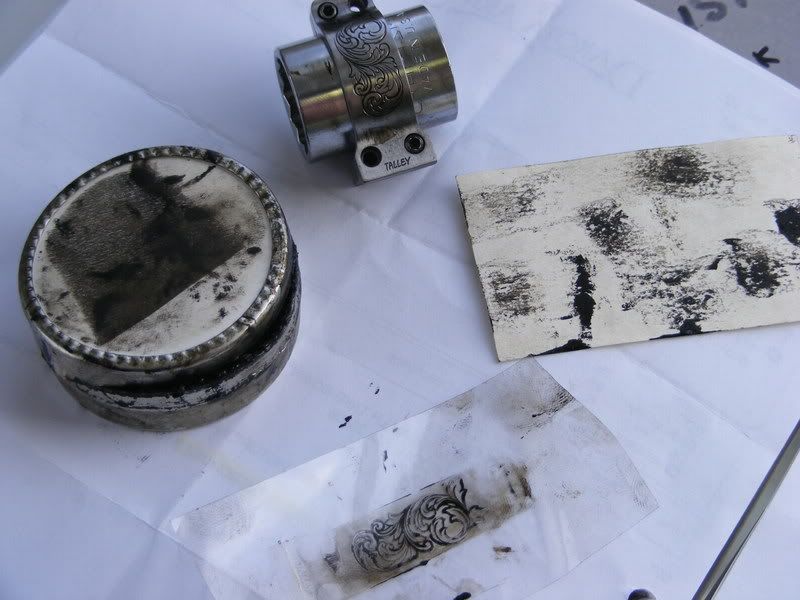
After I ink the original piece, I use the card to rub off the excess ink. I then apply clear packing tape, and burnish heavily, to lift the ink.
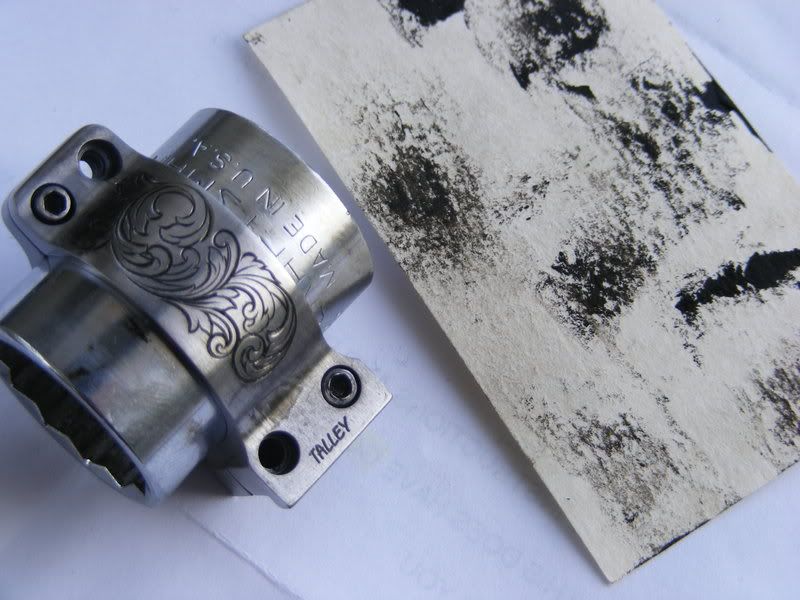
Then I pull the ink with the tape,
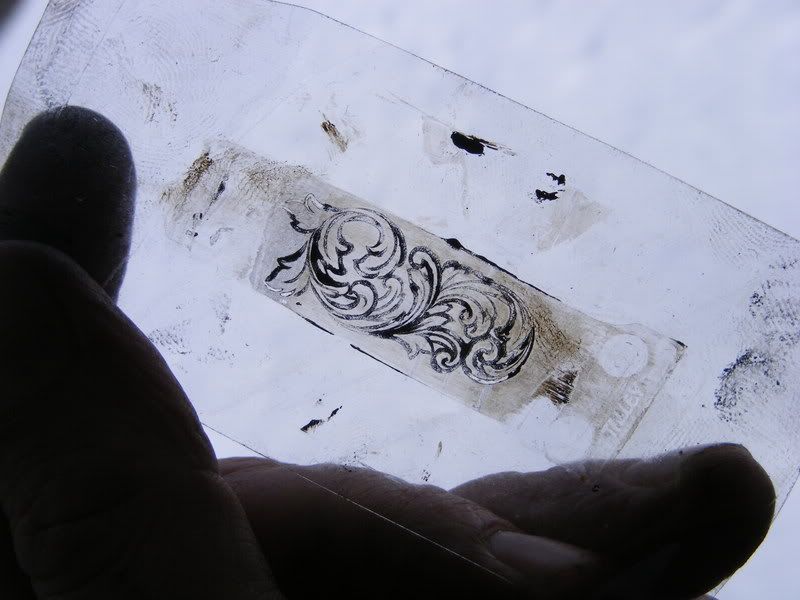
And place it on the next ring, and burnish lightly to transfer the ink,
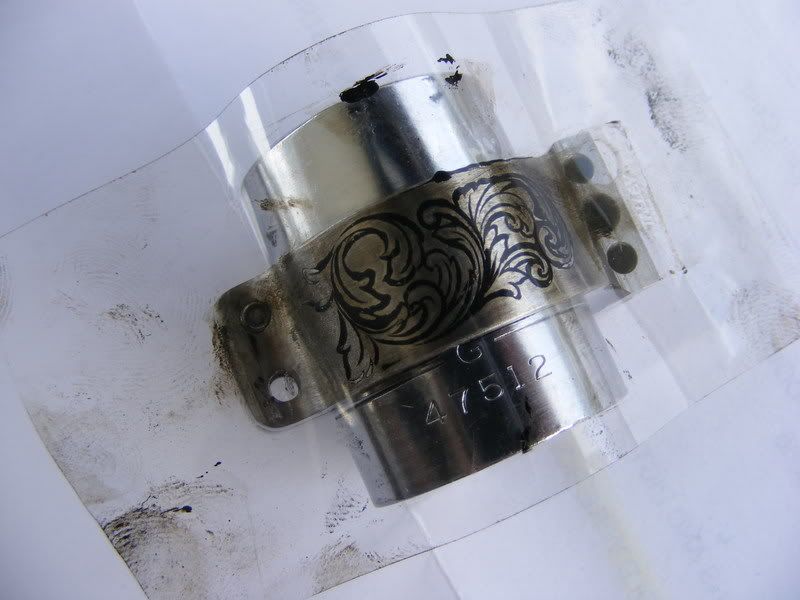