silverchip
~ Elite 1000 Member ~
Yesterday I started a new project for an upcoming show. I am using sheet silver that I made myself for this Little Stubby Whiskey Flask. I thought it might be fun to post a little progression as time goes by.
And yes I was watching Sams engraving video when I took the photo of the flask sitting on my bench!!!!
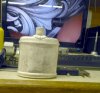
And yes I was watching Sams engraving video when I took the photo of the flask sitting on my bench!!!!
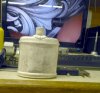