Alison Harman
Member
- Joined
- Apr 13, 2020
- Messages
- 17
I built mine following the parts lists found on youtube. Particularly the posts by Shaun Hughes and Rick Alexander. I chose the higher amp capacity power supply and added two cabinet fans.... one pushing, the other pulling, to vent the box to prevent the modified compressor from overheating. Added a disc drive power hone (sucks) and a digital speed control. The problem with the pump conversion is the piston seal.
The thin plastic seal is fine for airing up a tire from time to time. It is a one piece piston and connecting rod design that causes it to rock when running. Unlike a car's piston that only moves in a linear direction, the sides of the compressor piston travel a shorter distance than the ends a little. This causes seal failure on the ends. The donor compressor unit was never designed for extended continuous use.
The first time I lost compression I purchased a replacement compressor and gutted it for the piston. A month later I was experiencing compression seal wear again. Talking with Shaun about the problem, he was experiencing the same issue. He was tinkering with forming a better seal out of thermoplastics. I came up with my own solution. I got my idea from my antique bicycle's pump!
After removing the piston, I cut away the seal and removed the retaining washer holding it in place. Using the outside of the pump's cylinder and the inside of the retaining washer as templates, I cut a new seal from tight grain 1 1/2mm kangaroo hide. We use kangaroo for falconry because of its durability and it was handy. Goatskin or even cowhide will work. I soaked the leather in mineral oil and reassembled it into the pump. The key is making sure the leather seal's finished side is face up on the piston and extra diameter is pointing upward when assembling. This way the compression pushes the leather seal tighter against the cylinder wall on the upward power stroke.
Three months later, cutting daily for hours each day, the seal is still intact, strong and providing ample power for driving the handpiece. Hope this helps.
The thin plastic seal is fine for airing up a tire from time to time. It is a one piece piston and connecting rod design that causes it to rock when running. Unlike a car's piston that only moves in a linear direction, the sides of the compressor piston travel a shorter distance than the ends a little. This causes seal failure on the ends. The donor compressor unit was never designed for extended continuous use.
The first time I lost compression I purchased a replacement compressor and gutted it for the piston. A month later I was experiencing compression seal wear again. Talking with Shaun about the problem, he was experiencing the same issue. He was tinkering with forming a better seal out of thermoplastics. I came up with my own solution. I got my idea from my antique bicycle's pump!
After removing the piston, I cut away the seal and removed the retaining washer holding it in place. Using the outside of the pump's cylinder and the inside of the retaining washer as templates, I cut a new seal from tight grain 1 1/2mm kangaroo hide. We use kangaroo for falconry because of its durability and it was handy. Goatskin or even cowhide will work. I soaked the leather in mineral oil and reassembled it into the pump. The key is making sure the leather seal's finished side is face up on the piston and extra diameter is pointing upward when assembling. This way the compression pushes the leather seal tighter against the cylinder wall on the upward power stroke.
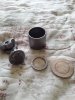
Three months later, cutting daily for hours each day, the seal is still intact, strong and providing ample power for driving the handpiece. Hope this helps.